内径超深溝加工
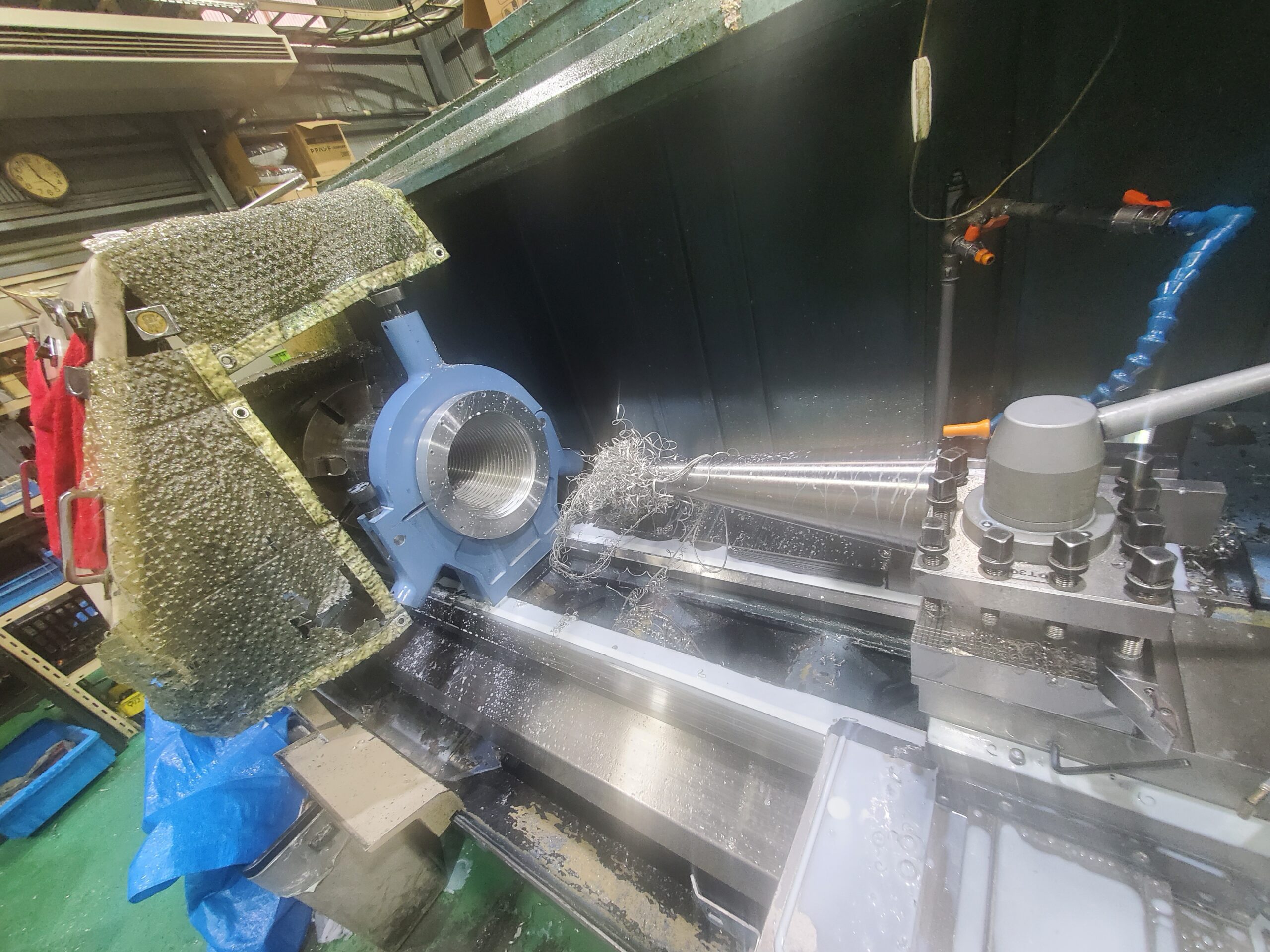
内径の深溝加工って難しいですよね。。。
見積段階では厄介な製品だなぁ、と思っていましたがなんとなく頭の中では加工できると思ったんですよ。
こんな工具でこんな刃物でこういったアプローチで、ってね。
いかに浅はかだったか、と気づいときは既にアフターカーニバル。
実際に加工が始まり内径の溝に差し掛かった時のあの絶望。
筆舌に耐えがたい苦しみを味合わせて頂きました。
形状は詳細割愛しますが、300φで長さ400ミリ位。
その内径に階段状に穴がありましてその階段毎に内径の深溝加工。
その数40本。
し・か・も
内径溝の深さが径で70ミリ!!!
し・か・も
最奥部分が70φの穴だったので溝は140φ。
し・か・も
めっちゃ薄肉。。。
・・・
・・・・
・・・・・
本ブログを読んで頂いている御仁方はわかると思いますが、先端のホルダーが35φに刃物突き出し35ミリとなるわけですが、そのホルダー長さ380ミリ。
え、12D!?
と相成りまして。
紆余曲折がありすぎて涙でキーボードが見えませんが、兎にも角にも完成に至りました。
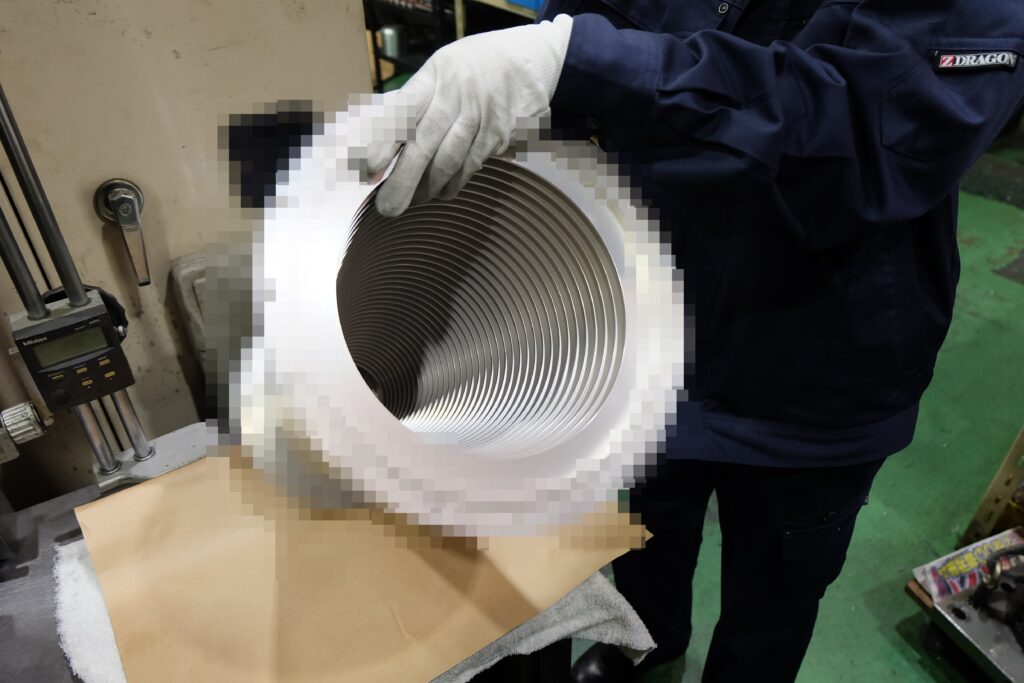
詳細アップしたいところですがこの写真で勘弁してください。
で、ホルダーの写真。
刃物は手研ぎでしたが、選定にめっちゃ時間掛かりました。
ここに書きたいところですが、その失敗?が技術となりましたので割愛させて下さい。
結局決め手は刃物だったのですが、そこにたどり着くために社員総出で挑みました。
刃物の形状、材種はもちろんクランプの仕方まで。
ホルダーも同じく悩みまして。
機械そのものが振動きつくて防振のホルダーを自分たちで作ろうか、なんて話まででていたんですよねぇ。。。
とかなんとか言いながらも。
次の壁は加工です。
階段状でその階段毎に溝深さが変わりますのでえげつない量のプログラムになってしまいますのでCAMで動かしたのですがその量、荒加工の15%くらいで20000ワード・・・。果てしない形状に挑んでいました。
切粉の排出にも手間を加え、刃物・ホルダー・プログラム・とボタンを押す私と社員みんなの思いを胸に加工完了できました。
測定も機上測定だったのですがそれでもかなりの精度でできていたので大満足。
御客様からエンドユーザー様の話を聞けたのですがとても喜んでくれていたようなので一安心。
これで深溝加工屋として頑張るでー、と言いたいところですが本当に技術が自分に入ってくれた素晴らしい製品でしたね。
検査終わって発送するまで1μも気を許されなかった製品でしたが現場みんなで集まって「このやり方は?」「こっちがよくない?」「こんなんどうでしょう?」と全員で煮詰めてた道中は個人的に泣きそうなくらいいい会社だな、と感動を覚えていました。それだけみんなが一生懸命考えてくれてるので自分がキチンと作らなきゃ、と帯を締めまくって鬱血しながら2月を過ごしておりました。
株式会社テラダは内径超深溝加工ができた(奇跡的?)八尾市の加工屋でございます笑
-
前の記事
2階完成 2021.03.02
-
次の記事
インコネルをこねくり回す 2021.03.20